Why do machine tools need to be passivated?
- Categories:Company News
- Author:
- Origin:
- Time of issue:2020-06-15 17:52
- Views:
Summary:As the saying goes, "Workers must first sharpen their tools if they want to do well". This principle has been well continued and spread from ancient times to the present. However, in the machine tool industry, the tool does not seem to be as fast as possible. When it comes to machine tools, there is a question, "Why do good tools need passivation?" Today, let us learn about "tool passivation". In fact, tool passivation is not what everyone understands literally, but a means to effectively improve tool life. Through smoothing, polishing, deburring and other processes to achieve the purpose of improving the quality of the tool. This is actually a normal process after the tool is finely ground and before the coating. Generally speaking, the methods of tool passivation and polishing are divided into brush, sandblasting, and drag polisher. Among them, brush and drag type are widely used. Anyone in the metal cutting industry knows that the tool will be sharpened by a grinding wheel before the finished product, but the sharpening process will cause different degrees of microscopic gaps. This causes the micro-notch to be easily expanded while the CNC machine tool is performing high-speed cutting, thereby accelerating tool wear and damage. Modern cutting technology has strict requirements on the stability and precision of the cutting tool. Therefore, the CNC cutting tool must be passivated before coating to ensure the firmness and service life of the coating. The advantages and purpose of tool passivation 1. Resistance to physical wear of the tool In the cutting process, the tool surface will be gradually worn by the workpiece, and the cutting edge is also prone to plastic deformation under high temperature and high pressure during the cutting process. The passivation treatment of the tool can help the tool to increase the rigidity and avoid the tool from losing its cutting performance prematurely. 2. Maintain the finish of the workpiece Burrs on the cutting edge of the tool will cause the tool to wear and the surface of the machined workpiece will become rough. After passivation treatment, the cutting edge of the tool will become very smooth, the phenomenon of chipping will be reduced correspondingly, and the surface finish of the workpiece will be improved. 3. Convenient for groove chip removal Polishing the tool groove can improve the surface quality and chip removal performance. The smoother the surface of the groove, the better the chip removal, and more consistent cutting can be achieved. After the cutting tool of the CNC machine tool is passivated and polished, there will be many small holes on the surface. These small holes can absorb more cutting fluid during processing, which greatly reduces the heat generated during cutting and greatly improves the cutting speed. . To sum up, the dullness of the blade edge is very important. As the ancients in my country said, "The bank of a thousand miles collapsed in an ant nest." Although the micro-notch on the blade edge is small, it affects the performance and life of the tool. "Thousands of miles" is a big issue that cannot be underestimated. Blade edge passivation technology is one of the effective measures to improve tool life and reduce tool consumption. It is feasible and effective in both economic and technical aspects. It will further promote the improvement of my country's cutting processing level and narrow the gap in cutting performance with foreign tools.
Why do machine tools need to be passivated?
Summary:As the saying goes, "Workers must first sharpen their tools if they want to do well". This principle has been well continued and spread from ancient times to the present. However, in the machine tool industry, the tool does not seem to be as fast as possible. When it comes to machine tools, there is a question, "Why do good tools need passivation?" Today, let us learn about "tool passivation".
In fact, tool passivation is not what everyone understands literally, but a means to effectively improve tool life. Through smoothing, polishing, deburring and other processes to achieve the purpose of improving the quality of the tool. This is actually a normal process after the tool is finely ground and before the coating. Generally speaking, the methods of tool passivation and polishing are divided into brush, sandblasting, and drag polisher. Among them, brush and drag type are widely used.
Anyone in the metal cutting industry knows that the tool will be sharpened by a grinding wheel before the finished product, but the sharpening process will cause different degrees of microscopic gaps. This causes the micro-notch to be easily expanded while the CNC machine tool is performing high-speed cutting, thereby accelerating tool wear and damage. Modern cutting technology has strict requirements on the stability and precision of the cutting tool. Therefore, the CNC cutting tool must be passivated before coating to ensure the firmness and service life of the coating.
The advantages and purpose of tool passivation
1. Resistance to physical wear of the tool
In the cutting process, the tool surface will be gradually worn by the workpiece, and the cutting edge is also prone to plastic deformation under high temperature and high pressure during the cutting process. The passivation treatment of the tool can help the tool to increase the rigidity and avoid the tool from losing its cutting performance prematurely.
2. Maintain the finish of the workpiece
Burrs on the cutting edge of the tool will cause the tool to wear and the surface of the machined workpiece will become rough. After passivation treatment, the cutting edge of the tool will become very smooth, the phenomenon of chipping will be reduced correspondingly, and the surface finish of the workpiece will be improved.
3. Convenient for groove chip removal
Polishing the tool groove can improve the surface quality and chip removal performance. The smoother the surface of the groove, the better the chip removal, and more consistent cutting can be achieved.
After the cutting tool of the CNC machine tool is passivated and polished, there will be many small holes on the surface. These small holes can absorb more cutting fluid during processing, which greatly reduces the heat generated during cutting and greatly improves the cutting speed. .
To sum up, the dullness of the blade edge is very important. As the ancients in my country said, "The bank of a thousand miles collapsed in an ant nest." Although the micro-notch on the blade edge is small, it affects the performance and life of the tool. "Thousands of miles" is a big issue that cannot be underestimated. Blade edge passivation technology is one of the effective measures to improve tool life and reduce tool consumption. It is feasible and effective in both economic and technical aspects. It will further promote the improvement of my country's cutting processing level and narrow the gap in cutting performance with foreign tools.
- Categories:Company News
- Author:
- Origin:
- Time of issue:2020-06-15 17:52
- Views:
Scan the QR code to read on your phone
Latest News

No matter how old you are, long live goddess day!

Congratulations on the successful revision of the official website of 8188www威尼斯!

Why do machine tools need to be passivated?

How to reduce surface cracks while processing cemented carbide
Contact
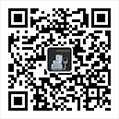
Scan and follow us
Messages